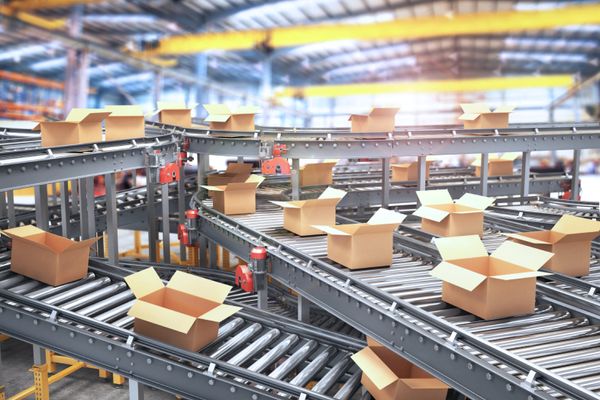
Автор статьи, Роман Аксененко, руководил разработкой и внедрением одного из первых в стране отборочных конвейеров. Сегодня он делится своим опытом с нашими читателями.
Практически все складские комплексы рано или поздно сталкиваются с тем, что их пропускная способность уже не может справляться с тем объемом продукции, который через них проходит. Из этой ситуации можно выйти двумя путями: первый — это увеличение складских площадей, набор дополнительного персонала и приобретение дополнительной складской техники, второй – это пересмотр существующих алгоритмов работы склада и их изменение или же внедрение новых технологий для складских процессов.
Как показывает практика, при складской обработке грузов больше всего времени тратится на перемещение отборщика между местами хранения. Чтобы уменьшить это время могут быть применены различные методы организации склада, как правило они связаны с уменьшением расстояния между наиболее часто используемыми местами хранения.
Один из методов — это динамическое хранение. Для его реализации с заданной периодичностью осуществляется анализ размещения продукции на складе по местам хранения и выполняется перемещение товаров таким образом, чтобы те товары, которые чаще всего отбираются, стояли в начале пути отборщика, а менее востребованные - в конце. Таким образом минимизируется путь отборщика по складу. Минусом данного метода является дополнительная нагрузка на работников склада, осуществляющих перемещение товаров и пополнение мест хранения.
Еще одним способом уменьшить «пробег» отборщика является параллельная отборка товаров по нескольким накладных одним отборщиком. Как правило такой способ отборки приводит к большому количеству ошибок при отборке товара.
Мелкоштучные товары могут быть размещены в отдельных секциях с местами для хранения маленького размера. При неправильной конфигурации склада такие секции обычно размещают в неудобных для обычной отборки зонах.
Для уменьшения «пробега» отборщика между рядами могут быть сделаны дополнительные проходы, но каждый такой проход уменьшает количество мест хранения в ряду.
После сборки заказа отборщик должен поместить отобранный заказ в зону комплектации. Расстояние между местом, где отборщик закончил отборку и зоной комплектации может быть значительным и, следовательно, перемещение отобранного заказа в зону комплектации может занимать много времени.
Еще один существенный фактор, влияющий на время отборки заказа, — это механизм отборки. Отборку можно проводить по бумажным накладным или с помощью терминала. Терминал может быть со сканером штрих кода или без него, находиться в руке у отборщика или быть закрепленным на его руке.
Все перечисленные выше, и еще множество других проблем, мешающих складу быстро и качественно производить обработку товаропотока, решает установка конвейерной линии в зоне отборки и комплектации товара.
Как это работает? Конвейером управляет специализированное программное обеспечение. В качестве входных параметров оно использует данные о товарах, которые нужно отобрать, и выводит данные о том, что в итоге собрано и укомплектовано. Как только данные вводятся в программу управления конвейером, она рассчитывает необходимое количество коробов для отборки и определяет, какой товар в какой короб будет отобран. Если в местах хранения не хватает товара для отборки согласно накладной, отправляется команда на их пополнение. Как только места хранения будут пополнены запустится процесс отборки товара. В начале конвейерной линии стоит модуль, который из сложенной тары складывает и скрепляет липкой лентой короб. На короб сразу же наклеивается стикер с данными о накладной и уникальным штрих-кодом. На всех этапах последующего движения этого короба по конвейеру этот штрих-код будет использоваться для его идентификации. Далее короб начинает движение по конвейерной ленте к станции отборки, на которой находится товар для этого короба. Станция отборки является рабочим местом отборщика. Она представляет собой зону, в которую заходит конвейерная лента. В центре станции отбора располагается отборщик, со всех сторон вокруг него находятся места хранения. Места хранения представляют собой плоскости из роликовых направляющих, расположенных под углом, и имеют разный размер для различных товаров. В тот момент, когда отборщик берет товар с места хранения, товар, находящийся за ним, благодаря наклону и роликовому полотну, сдвигается вперед и перемещается на передний край места хранения. Такой принцип организации мест хранения называется гравитационным, поскольку подача товара для отборки осуществляется естественным образом за счет действия силы тяжести. Пополнение мест хранения производится с обратной стороны стеллажа, таким образом пути отборщика и сотрудника, занимающегося пополнением мест хранения, не пересекаются. При попадании короба на станцию отборки на каждом месте хранения, с которого необходимо отобрать товар, загорается индикатор с изображением количества товара, которое необходимо отобрать. На каждом месте хранения также есть кнопка, которую необходимо нажать после отборки товара. После отборки всего необходимого товара с места хранения конвейер проверяет правильность отборки при помощи весов, встроенных в часть конвейерной ленты, на которой стоит короб во время отборки на станции отбора. После этого, если вес короба соответствует расчетному, он выезжает со станции отбора обратно на конвейерную ленту и перемещается на следующую станцию отбора. После отбора всех товарных позиций в короб он по конвейерной ленте перемещается в зону комплектации. Там отобранные короба объединяются согласно накладным и размещаются в соответствующие зоны в соответствии с направлением, в котором они будут отгружаться.
Применение конвейерной технологии при отборке и комплектации товара решает огромное количество проблем, которые возникают при классической отборке товара на складе. Отборщик фактически находится на одном месте и не тратит время на перемещение по складу. У него ничем не заняты руки, благодаря чему он может максимально быстро отобрать товар. Места хранения, из которых нужно отобрать товар и необходимое количество товара для отборщика интуитивно понятны, это сводит к минимуму возможные ошибки при отборке, а дополнительная проверка отборки по весовым характеристикам товара сводит вероятность ошибки практически к нулю.
Таким образом, использование конвейера для складской обработки товара увеличивает пропускную способность склада, существенно снижает количество ошибок в отборке товара и снижает затраты склада за счет уменьшения работников склада, производящих отборку. В результате многие крупные торговые сети России уже по достоинству оценили все преимущества от использования конвейеров для складской обработки товаров и активно внедряют эту инновационную технологию.
Роман Аксененко,
Специалист по транспортно-складской логистике
10.04.2019