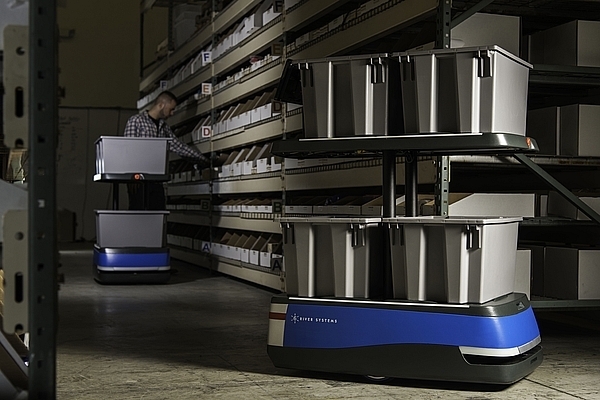
At LogiMAT 2019, American logistics start-up 6 River Systems is presenting the future of warehouse automation: In Hall 1, Stand K37, the company’s collaborative picking robot Chuck will make its European debut. 6 River Systems’ AI-powered solution makes pickers faster and more accurate, and enables a 200 to 300 percent increase in pick rates over manual carts. Chuck can be integrated into any warehouse within a month. The flexible nature of collaborative robotics allows warehouses to add additional Chucks to cover seasonal demand at short notice. That’s why this US start-up’s solution is an appealing, cost-effective alternative to classic warehouse automation solutions.
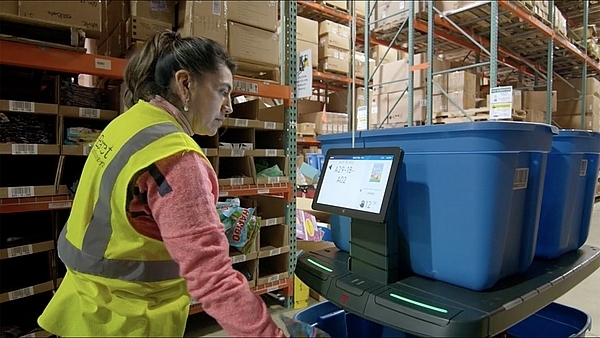
Invented by former Kiva Systems (now Amazon Robotics) executives, Chuck is the world’s only collaborative robot that leads pickers through their work. Chuck’s special features include the largest carrying capacity of any fulfillment robot, a configurable setup that supports the most diverse range of SKUs and quick deployment into any warehouse.
Chuck is a more collaborative and adaptive alternative to traditional warehouse automation, which is complex and financially risky, requiring extensive design, installation and expensive maintenance fees. With 6 River Systems, logistics operators now have an option for flexible automation that requires no additional infrastructure and is compatible with any WMS.
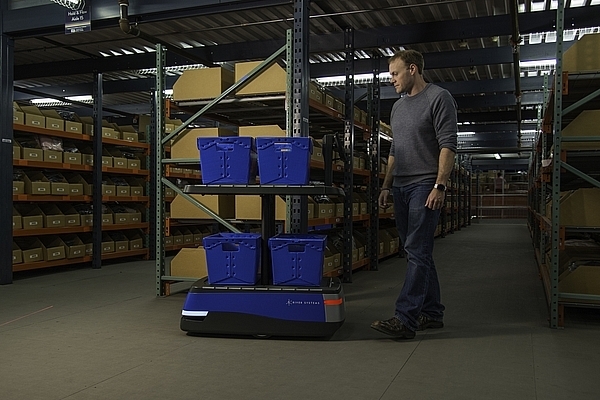
How Chuck works
The 6 River Systems solution eliminates long walks, reduces in-aisle walking and makes picking tasks faster. It is powered by robots (Chucks) and cloud-based software. A fleet of Chucks work collaboratively with associates to boost three warehouse operations: induct, picking and takeoff.
Induct - Chuck communicates with the software to intelligently group orders to minimize walking and maximize productivity. A worker puts boxes or shipping containers on Chuck and then Chuck travels on its own to meet pickers in the picking area.
Picking - Once badged in, Chuck leads pickers through a group of tasks (put-away, picking, counting, replenishment and sorting). Chuck shows pickers important data — item image, description, quantity, location, etc. — on a tablet-sized display. Chuck’s built-in scanner captures all product information, including real-time validation of lot and serial number.
Takeoff - Once fully loaded, Chuck informs pickers where to find the next Chuck, and then travels on its own to the next destination. The destination can be take-off for packing, a separate pick zone or an exception area to fix problem orders. At takeoff, a worker unloads Chuck and prepare orders for shipment. The now-empty Chuck heads back to induct, where the cycle begins again.