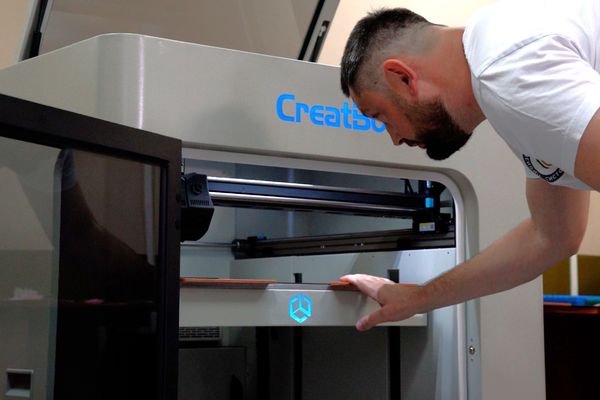
Компания ОТЭКО, оператор морских терминалов в порту Тамань, активно осваивает аддитивные технологии. За два месяца в новом цехе 3D-печати изготовлено уже 90 деталей для замены изношенных узлов оборудования, а в производственной очереди находится ещё около 1 000 изделий.
3D-печать как инструмент ускорения ремонтов и снижения затрат
В ОТЭКО внедряют послойное наплавление пластиковых нитей для создания прототипов и полноценных рабочих деталей. Такой подход позволяет:
-
оперативно воспроизводить необходимые запчасти;
-
адаптировать изделия под конкретные технические требования;
-
минимизировать время простоя оборудования;
-
снизить затраты на обслуживание и ремонт.
По словам ведущего инженера-технолога ремонтно-механического цеха Виктора Баусова, использование 3D-печати обеспечивает экономию ресурсов, сокращает время на изготовление и исключает необходимость полной замены дорогостоящих агрегатов. Например, для кондиционеров в вахтовых автобусах были оперативно напечатаны шестерёнки, что позволило быстро восстановить работу систем охлаждения.
Планы на расширение и новые горизонты применения
ОТЭКО уже сформировала план расширения использования 3D-печати на ближайший год. В перспективе:
-
внедрение технологий печати с активной камерой для более точного воспроизведения сложных деталей;
-
использование 3D-сканеров для ускорения создания цифровых моделей;
-
переход к изготовлению металлических запчастей для более широкого спектра применения.
Инженеры по контрольно-измерительным приборам и автоматике стали одними из первых, кто оценил преимущества новой технологии. Так, на конвейерных линиях навалочного терминала встал вопрос регулярной замены держателей тросов датчиков контроля порыва ленты — до 50 штук ежегодно. Заказать их как отдельные запчасти невозможно, поэтому специалисты напечатали их самостоятельно. Опытная эксплуатация подтвердила полное соответствие геометрии и прочности изделия требованиям оборудования.
«Детали, напечатанные на 3D-принтере, показали отличные результаты. Точная подгонка и надёжность позволили нам не только решить проблему с износом, но и сократить сроки восстановления оборудования», — подчеркнул Евгений Поляков, ведущий инженер по КИПиА ОТЭКО.
Инновации в производственной культуре
Отдельно стоит отметить, что запуск 3D-печати в ОТЭКО стал возможен благодаря корпоративной программе «Есть идея!». Этот инструмент вовлекает сотрудников в улучшение производственных процессов и условий труда. Инициатива позволила оперативно внедрить новые технологические решения и продемонстрировать реальные эффекты от инноваций.
В долгосрочной перспективе 3D-печать станет для ОТЭКО не только средством оперативного ремонта, но и частью стратегии по комплексной модернизации производственной базы. Компания планирует увеличить количество напечатанных изделий, расширить их номенклатуру и продолжить снижать расходы за счёт локализации производства комплектующих.