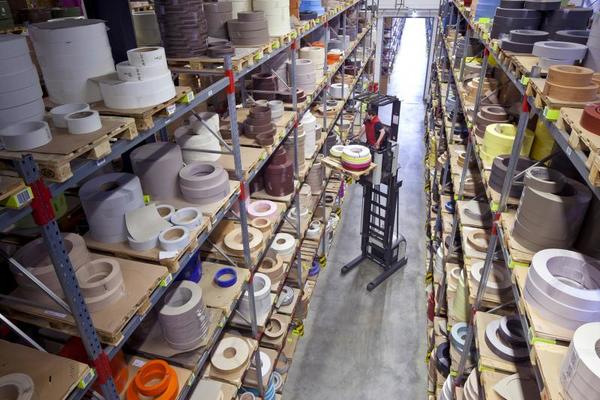
The distribution warehouse operated by Rudolf Ostermann GmbH in Bocholt, Germany, processes up to 3,000 orders per day.
This makes Ostermann Europe's leader for edgings and fittings. Part of the recipe for success is a distinct focus on service. Ostermann guarantees customers that all orders will be processed and shipped by 4:00 p.m. on the day the order is received. 33 UniCarriers forklifts ensure that orders are picked rapidly and loaded on trucks on time. Last year, the mail order company signed a full-service contract for the entire fleet that includes preventive maintenance, UVV accident prevention audits as well as spare parts supplying. Ostermann thus provides constant high availability of the forklifts and costs are predictable.
Everything at Ostermann is about edgings. They are the wholesaler's main product range for carpenters and cabinet makers. At the 14,000 m² logistics center, rolls of edgings are stocked in a wide range of widths, colors and decors - in addition to other articles such as fittings, sliding doors or shutter systems. Buyers are carpenters and cabinet makers throughout Europe. Ostermann processes up to 3,000 orders every day for their 30,000 customers. The 45 forklift drivers pick up to 4,500 orders every day. The foundation of this output is a functioning and reliable fleet of forklifts. 31 warehouse trucks and two counterbalance trucks from UniCarriers make the operators' work easier. "Because all our order picking is manual, logistics here depends entirely on the smooth operation of the forklifts," Christof Wauters, head of Logistics and Materials Management at Ostermann, explains. "That is why the requirements for the suppliers of our forklift trucks are so strict. UniCarriers not only offer us a convincing price-performance ratio, they also provide us with a service concept customised to our particular needs." Over the years, the edging specialist has also looked at other suppliers on the market – but in the end, they have repeatedly decided to stick with Atlet, now UniCarriers.
Forklifts as the heart of logistics
With the exception of the fully-automatic high-bay warehouse which serves as a storage warehouse and is equipped with two stacker cranes, the forklift trucks are used everywhere in the distribution center. The heart of logistics is the manual order picking warehouse with a total of 12,000 pallet storage locations. When replenishments are needed, eight UniCarriers TERGO reach trucks type UNS and UMS for loads of up to 2,000 kg go into action. They collect pallets at the warehouse's stock removal zone and store them in the assigned places in one of the six tiers. Order picking in the 15-aisle pallet warehouse is done by 17 type OPS 100 high-level picker trucks. The forklift drivers put together between one and eight customer orders during one passage. In the process, they rise to heights of up to 8m with the order pickers. Ostermann operates a separate warehouse zone for long loads such as sliding doors and shutter systems. The articles are up to 6m long, account for 10-15 percent of sales and are stored in mobile racks. For easy and safe transport, a TERGO UFS type four-way reach truck is used. A standard feature of the truck is a function that adjusts the distance between the hydraulic forks so that products of different dimensions can be picked up flexibly as well as stored and retrieved. The mobile racks are moved to allow the forklifts to drive down the aisles. In the dispatch area, five manoeuvrable ERGO XJN 100 type sit-on stackers simplify handling. Two QX2 and TX3 type electric counterbalance trucks round off in-company logistics and load the pallets with packages ready for shipment onto trucks.
Speed as a distinguishing feature
Part of the Ostermann corporate philosophy is strong customer orientation. In addition to staging edging systems in short lengths or small batches on request, this also means processing orders rapidly. Within the framework of their 24h delivery service, the company guarantees that orders are delivered by 4:00 p.m. the next day. The delivery capability of this just-in-time service is 97 percent. "Sometimes there is no more than an hour between order entry and dispatch because the trucks are at the door no later than 5:15 p.m.," explains Christof Wauters. "About that time, we are running at full throttle in the warehouse. It only works when all processes are optimally coordinated." Fleet performance and availability are decisive for the efficient flow of materials. Most trucks run during the entire shift and reach speeds of up to 14 km/h when transporting in-house. To prevent accidents, a high standard of safety is a must. With good driving stability, optimal all-round visibility, and a tilt function for the mast, the TERGO trucks meet the high requirements of intense stock handling. The mail order company also saves valuable time thanks to the long battery life of the electric equipment which is capable of running for an entire shift without any charging.
Full service for full performance
To further optimise the use of their equipment, Ostermann signed a full-service agreement last year for the entire fleet. It includes a flat rate for maintenance including the annual accident prevention (UVV) audits, spare part supplying and replenishment as well as the exchanging of wearing parts as needed. "The agreement simplifies our fleet management," states Christof Wauters. "It used to be that we had to coordinate different suppliers for service, maintenance and spares supplying. We now handle everything centrally through UniCarriers. Thanks to the fixed amount of the flat rate maintenance fee, our costs have also become more transparent and plannable." Within the framework of the service agreement, Ostermann pays a fixed monthly installment for each truck based on age and intensity of use of the forklift trucks. On the basis of the operating hours it is also possible to determine whether a forklift has been used too intensively or too seldom. The aim is to keep the operating hours of all forklifts at a similar level to prevent individual trucks from premature wear. Another advantage of the all-round service package is the short response times in the event of a service incident: If a forklift breaks down or if a spare part is needed, a UniCarriers technician is on site within a matter of hours. Depending on how urgent it is, repairs are made the same day which minimizes standstills within the fleet. Forklift operators play an important role in peak performance within the warehouse, in addition to the trucks. "The well-being of our employees is very important to us," explains Christof Wauters. To minimize loads, we have limited the maximum weight per package to 30 kg, for example, and also place great importance on comfortable forklifts. Drivers ultimately spend their entire working day on the forklifts." An important plus point of UniCarriers trucks are thus their high ergonomic standards. Drivers adjust important parameters themselves, such as position of arm and back rests, seat and floor and can thus personalize their trucks. This not only helps keep the physical strain of an eight-hour shift to an absolute minimum. Recreating the settings when employees need to use a different truck also helps establish a familiar working atmosphere.
Results
Ostermann has profited from the concept of distinctive service orientation and short delivery times: In the last ten years, the company has doubled throughput in the warehouse and thus also the external sales volume. Thanks to their close contact to UniCarriers, Ostermann can also adjust the size of the forklift fleet to the order volume even at short notice. Moreover, the fleet is constantly updated by the regular replacement of older trucks with new ones. Consequently, Ostermann benefits from a fleet that is constantly state-of-the-art and provides maximum performance during a day's work. Due to the positive experiences in the main warehouse in Bocholt, the mail order company has decided to extend their cooperation with UniCarriers to their six foreign subsidiaries.