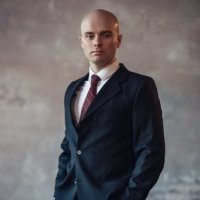
Last year I’ve participated in an excellent Lean Production training by Pavel Pashkov and Andrey Aleshin in Moscow Council of SCM professionals ruled by Yrysbek Tashbaev.
Honestly speaking, I was familiar with most of concepts and ideas like value stream creation, 5S, and steps for operations standardization, as I had been previously trained to use IWS tools by P&G, which have much in common with Lean, Kaizen and Goldratt methodologies. However, there was one point of extreme importance shown, proved and long discussed during that session, which I didn’t want to accept at once, as well as during the next several months. What is the point and why is it so important? It is a very simple 3-step approach to operations excellence. To succeed you must strictly respect the following step order:
- First — Standardization;
- Second — Optimization;
- Only last — Automation.
Even being very easy to realize, this concept always arouses great resistance. Myself and everybody I’ve tried to offer this approach at first refused to accept this way as the most effective. “How can “standardization” come first, if you intend to make optimization?” — the first question you’ll usually get when asking any production guy’s opinion. The first clue is that it is not possible to make optimization of the process, which exists without a standard. The second clue is that automation of process, which is not optimal brings you to automated over-processing.
Thinking about this concept now I remember P&G approach (whose methods became a benchmark for me forever) to any problem solving. If you got a mistake, while any operation execution, than ask yourself questions:
- Does the standard for this operation exist? If “no”, than stop and create a standard.
- Was the operation executed following the standard? If “no”, than stop, investigate and eliminate route cause. What was the reason for wrong execution? If it was discipline, than punish. If lack of knowledge, than train people. If it was a standard, which it is not possible to respect, than improve standard.
- If standard existed, was respected but a mistake nevertheless appeared, than investigate, find the route cause, eliminate it at the system level and then update your standard and train executors.
This approach is exactly about standardization and optimization. P&G believes a standard for a process is a must. So, you will never get any approve for optimization in the company unless you show how the standard changes and what is the exact profit for a company from this change. And to overpass to automation you just need to take optimized standard, describe ideal and future state and assess the effect.
Now I can see the mistake, which was previously adherent to. We all see automation as a peak form of optimization. But it is not. Moreover, in some cases automation is a form of deoptimization, which brings process to more losses that it was with people participants. As long as in our country labor cost is quite low and people are extremely creative, automation will not bring 100% savings in all operations where can be applied. As a result we can see a lot of cases in very big national and international businesses, where automation does not bring the level of satisfaction it initially promised.
Bogdan Golovanov, Logistics expert focused on operations excellence. Experienced in machinery production. B. Eng., M.Sc. & MBA.