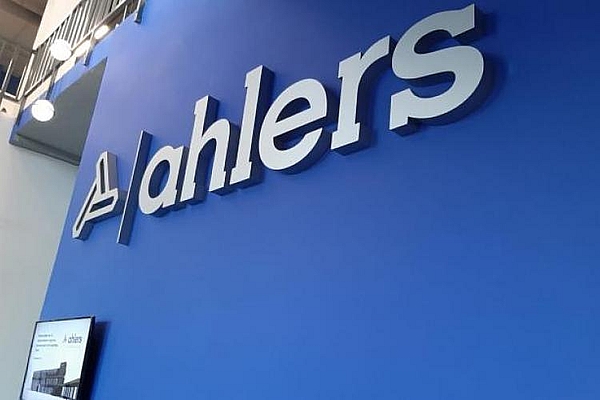
Транспортировка готовой воздухоразделительной установки — технически непростая задача. Установка состоит из 85-тонных модулей, а также 50 стандартных и крупногабаритных контейнеров, для производства которых используются материалы из 4 разных стран. Для перевозки столь масштабных систем приходится использовать как автомобильный, так и морской транспорт. О том, как осуществить такой проект эффективно — расскажем на примере работы Ahlers.
В чем заключалась работа?
Компания в Моглино (Особая экономическая зона, расположенная в Псковской области) заказала готовую воздухоразделительную установку у итальянского поставщика. Детали и материалы для такой установки производятся сразу в четырех странах: Италии, Испании, Турции и Корее. Общая масса поставленного оборудования составила около шести тысяч тонн, а для перевозки грузов из Италии, Испании и Турции было задействовано более 50 единиц транспорта — от стандартных грузовиков до специальных тралов для перевозки негабаритных грузов.
Наиболее крупные модули установки — два холодильных бокса, они производятся в Италии. Самый большой из них в длину 35 метров, ширину 5,5 метров и высоту 5 метров. Доставить такую крупную систему прямым маршрутом просто невозможно, так что сначала холодильные боксы были доставлены в итальянский порт Маргера, откуда их направили в российскую Усть-Лугу на зафрактованном судне. Уже оттуда модули погрузили в грузовики и доставили до Моглино.
Другие крупногабаритные боксы и контейнеры производились в Корее. Их путь с корейского Масана до Моглино проходил через бельгийский Зебрюгге до портов Северной столицы. По прибытии в Санкт-Петербург они были перегружены в грузовые автомобили и доставлены до конечной точки.
Сложности транспортировки крупных модулей
Логистика крупногабаритных модулей — трудоемкая задача, сложность которой растёт пропорционально размеру груза. У каждой автомобильной трассы есть свои ограничения по размеру и весу транспортируемых товаров. Обычно их ограничения зависят от наличия мостов, туннелей и иных строений, которые ограничивают объем перевозимых грузов.
Именно для таких случаев и есть водные маршруты. Так, основная часть крупногабаритного груза была отправлена через порт в Санкт-Петербурге и только потом перевезена в Моглино. Однако и морские пути не всегда могут полностью заменить сухопутный участок маршрута, что и произошло в случае поставки итальянских модулей.
При разработке маршрутов специалисты Ahlers выяснили, что на пути следования необходимо провести ряд сопроводительных работ. Речь идёт о преодолении переездов, подъёме линий электропередачи временной разборки части инфраструктуры. Из-за этого на преодоление сухопутного участка длиной в 250 км пришлось затратить 6 суток При этом, использовать питерский порт было невыгодно — резко росло количество альтернативных издержек. Впрочем, основной сложностью была транспортировка по территории России.
Казалось бы, выход есть — неподалеку находится порт Усть-Луга. Но обычно этот порт используется для поставок навалочных грузов и не располагает необходимым оборудованием для выгрузки крупных модулей. Именно для таких случаев и важно прогнозировать маршрут наперед. Поэтому команда Ahlers заранее спроектировала и сертифицировала специальные балки и растяжки, которые могли бы безопасно выдерживать подобный груз.
Уже в России на маршруте до Моглино оставалось последнее препятствие — несколько мостов по пути, для которых масса трейлера с грузом была слишком велика. В таких случаях есть только один выход — коммуникация с уполномоченными транспортными ведомствами. Так, Ahlers смог согласовать ряд строительных работ по установке временных эстакад, которые могли снизить нагрузку на мост. Такие работы прошли на трёх мостах в Псковской области, для чего ведомства перекрыли дорожный участок на некоторое время.
Транспортировка крупногабаритного груза по территории России — это проблемы не только организационного характера. Работа параллельно сопряжена с юридическими и процессуальными трудностями. Так, необходимо получать разрешений от местных властей и владельцев инфраструктуры на перевозку крупногабаритных модулей через туннели, города и мосты. Затем полученные разрешения предоставляются федеральным властям для получения окончательного разрешения на весь маршрут. Наличие локального представительства со знанием местных особенностей помогает упростить такой процесс.
Таможенные трудности
Ещё одним вызовом, который стоял перед проектом, стало прохождение таможни. Клиенту было особенно важно импортировать установку как единую производственную линию — в таком случае налог на импорт составил бы 0%.
Для этого было необходимо получить от Федеральной таможенной службы классификационное решение, которое позволяет импортировать детали конструкции под одним кодом ТН ВЭД. Таможенные специалисты Ahlers занимались подготовкой и подачей заявки на протяжении нескольких месяцев, а весь процесс постоянно пополнялся новыми видами документации. ФТС требует чрезвычайно точную информацию относительно деталей конструкции. Это касается как конструкции установки в целом, так и технических характеристик каждой импортируемой детали. По сути, они должны убедиться, что каждый компонент, каждая гайка или болт действительно необходимы для сборки производственной линии.
При этом, вся необходимая информация должна быть предоставлена Таможенной службе еще до фактического завершения закупки деталей. Это особенно сложно в подобных проектах, когда окончательный список компонентов может поменяться в любую минуту. Например, если нужные детали отсутствуют в продаже у одного поставщика, их необходимо заказать у другого. С уже утвержденным списком деталей, нужно будет пройти несколько дополнительных таможенных процедур, чтобы актуализировать его для получения класификационного свидетельства.
Вместо итога
Транспортировка крупногабаритных товаров — объективно сложный процесс, содержащий в себе множество неявных деталей. На кейсе работы Ahlers мы показали, что сложности с логистикой зависят не только от маршрута, но и от локальных особенностей: законодательства, связей с ведомствами и правил экспорта или импорта.