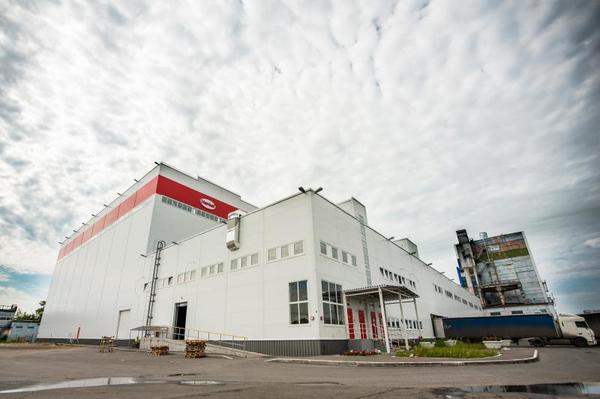
2 сентября 2013 года состоялась пресс-конференция «10 лет Jungheinrich в России». Алексей Вершинин, начальник отдела продаж системной техники, Jungheinrich в России и Сергей Гордиенко, руководитель отдела планирования и логистики Henkel в России, рассказали о проекте первого автоматического склада Jungheinrich в России - распределительном центре Henkel в Перми.
[[{"fid":"1903","view_mode":"default","type":"media","attributes":{"height":800,"width":531,"alt":"Сергей Гордиенко (слева) и Алексей Вершинин (справа)","title":"Сергей Гордиенко (слева) и Алексей Вершинин (справа)","class":"media-element file-default"}}]]
В работе пресс-конференции приняли участие член правления Jungheinrich AG Хельмут Лимберг (Dr. Helmut Limberg), вице-президент по продажам в Восточной Европе Михаэль Вайганд (Michael Weigand), генеральный директор Jungheinrich в России Штефан Деммиг (Stefan Demmig), руководитель отдела продаж Jungheinrich в России Люк Снайдерс (Luuk Snijders), начальник отдела продаж системной техники Jungheinrich в России Алексей Вершинин, руководитель отдела планирования и логистики компании Henkel в России Сергей Гордиенко.
Алексей Вершинин: Работа по созданию полностью автоматического склада компании Henkel, включая послепродажное обслуживание, началась в 2011 году.
Сергей Гордиенко: Вначале я вкратце расскажу о стратегии производства и снабжения подразделения «Чистящие и моющие средства» компании Henkel в России.
Почему Пермь? Мы считаем, что Пермь – это стратегическое место в географии России. С одной стороны, Пермь находится близко к Уральским горам, но пока еще в Европейской части. И, тем самым, этот город близок к 70% наших клиентов, которые живут в европейской части России. И, тем не менее, сосредоточены на 30% территории. Если мы посмотрим за Урал, то это Сибирь, Дальний Восток, Азиатская часть России, то это 70% территории и 30% населения. Таким образом, получается, что мы близки к нашим клиентам по нашему расположению. Второе, мы близки к источникам сырья и упаковки. И, самое важное – это наш самый большой завод подразделения «Чистящие и моющие средства» в России.
Почему компании Henkel в России нужно было построить завод, а затем и склад в этом месте? Несмотря на то, что, как я уже упоминал, это самый большой завод подразделения «Чистящие и моющие средства» в России, долгое время там был и самый маленький склад. Объемы производства за несколько прошедших лет выросли в 3-4 раза. И такой рост объемов производства требовал увеличения складских площадей. В итоге, руководство компании Henkel приняло решение инвестировать в собственные складские площади около 14 млн. евро, что составляет примерно 500 млн. рублей.
Почему это решение мы реализовали совместно с компанией Jungheinrich?
Первое – это ориентированность на клиента. Компания полностью нацелена и замотивирована на достижение конечного результата – запуск проекта совместно с Henkel.
Второе – любые запросы, которые у нас появлялись в процессе проектной разработки, мы адаптировали и применяли в режиме online.
Следующий немаловажный фактор - по мнению проектной группы, компания Jungheinrich на 110% соответствовала всем нашим требованиям. Конечно же, компания устроила нас и по степени удовлетворения наших коммерческих требований.
Сроки проекта были весьма сжатые, и компания вписалась под них.
Были выполнены и учтены все наши технические условия и другие специальные требования.
Для России, особенно на Урале (в Перми) очень важен и такой фактор, как обслуживание построенного склада. В то время у компании Jungheinrich уже была команда в Перми, которая обслуживала погрузчики и другую стандартную складскую технику. Мы знали эту команду и верили ей. И эта команда была успешно обучена вместе с нашей командой работе с автоматическим складом и ее эффективному обслуживанию. И она с успехом справляется с этой задачей.
Алексей Вершинин: Хочу немного рассказать про сроки реализации данного проекта.
Первый контакт был в феврале 2010 года, а ввод склада в эксплуатацию - в феврале 2012 года. Всего два года прошло между этими двумя датами.
Вначале (в марте 2010 года) мы разработали концепцию. В июле мы передали Henkel детальное предложение. В августе получили устное подтверждение заказа на реализацию проекта. На согласование договора нам понадобилось 4 месяца (такой документ требует длительных обсуждений и согласований). И вот весной 2012 года мы начали поставки необходимого оборудования в Пермь. И ровно год спустя, 29 февраля 2013 года мы вместе с компанией Henkel торжественно праздновали открытие склада.
Сергей Гордиенко: Дата 29 февраля означает, что мы будем отмечать запуск склада раз в четыре года (смеется - примечание отраслевого портала "Логистика").
Алексей Вершинин: Как все это происходило? Задача была непростая. Мы должны были реализовать этот проект в течение очень небольшого времени. Сложности были не столько с таможней и поставкой товара. Были проблемы с погодой. Нужно было закончить реализацию проекта незадолго до начала зимы. Нужно было учесть все строительные нормы и требования. Более того, нам необходимо было завершить этот проект до окончания осени и потом заниматься его доводкой.
Сергей Гордиенко: Хочу немного рассказать про технические детали проекта. В первую очередь мы говорим о емкостях хранения 25 тысяч паллетомест. Высота хранения до 26 метров в автоматической части. И три крана-штабелера, обслуживающих эту складскую площадь.
Если говорить о входящих логистических потоках, то это конвейерная линия, полностью интегрированная с производством. Мы фасуем нашу готовую продукцию, например, «Персил», в упаковку. Дальше единицы готовой продукции формируются в короб. Далее по конвейерной ленте поступает на оборудование, где формируется готовый паллет, который по конвейеру поступает в склад. Мы, таким образом, говорим об интегрированной системе логистических потоков предприятий.
Также немаловажно, что у нас есть зоны, где мы дорабатываем продукцию для промо-активностей, это тоже было включено в технические параметры проекта и успешно работает.
Если говорить о логистике исходящих потоков, то имеются 15 доков (ворот), 13 из них оснащены гравитационными накопителями.
Для нас также очень важно повышение эффективности. Мы покрываем все наши производственные пики, которые случаются, и обеспечиваем своевременную отгрузку готовой продукции нашим клиентам.
Алексей Вершинин: Действительно, склад обслуживают три крана-штабелера, установленные прямо на стеллажах. Они обрабатывают до 57 паллет в час в единичном цикле и 35 паллет - в двойном цикле.
Что касается потока товаров на складе - в начале конвейеры доставляют палеты из производственного цеха в зону высотного хранения. Далее один из кран-штабелеров доставляют палеты в предусмотренной программой управления канал.
Все это управляется системой Jungheinrich WMS.
Шаттловый механизм доставляет продукты в выбранном канале в определенную ячейку. Такой канал в глубину может вмещать до 10 паллет.
Мы уверены, что именно такой тип хранения был верным решением потому, что мы работаем с моющими и чистящими средствами, которые являются по сути довольно однородным грузом. Система хранения оказалась оптимальным решением, позволяющим использовать до 90% складских площадей.
После этого палета учитывается в WMS, снова подается краном-штабелером на конвейер, и по конвейеру попадает в область комплектования заказов. В районе ворот склада находятся гравитационные накопители. Такая гравитационная площадка вмещает 33 паллеты. Это соответствует количеству товара, которое вмещает в себя одна фура. Это решение позволяет сэкономить на погрузочной технике и, кроме того, сокращается путь палеты со склада до фуры.
Склад имеет возможность расширения для следующей очереди строительства.
Также имеется зона ручной обработки, в которой работают около 15 арендных погрузчиков Jungheinrich. Получается, что весь ассортимент складской техники – из одних рук.
Все это обслуживается системой Jungheinrich WMS. Это собственный продукт компании Jungheinrich, и все компоненты склада управляются этой программой.
Сергей Гордиенко: Хотел бы отметить, что WMS от компании Jungheinrich очень интуитивная и понятная. Ей легко обучаться. Самое главное – это гибкое решение. Склад – живой организм. Ситуация, материальные потоки, ассортимент меняются. WMS можно гибко адаптировать к меняющимся условиям.
Второе, что я хотел отметить – это повышение уровня качества обслуживания наших клиентов. Это очень важный фактор, которого позволил достичь это решение.
Третье преимущество – это оптимизация структуры производства и снабжения подразделения «Чистящие и моющие средства» компании Henkel в России.
Четвертое преимущество – вклад склада в устойчивое развитие. Это решение (автоматический склад, оптимизация структуры производства и снабжения подразделения «Чистящие и моющие средства») позволило компании Henkel снизить выброс углекислого газа в атмосферу в 360 тыс. кг в год. Мы сократили пробег автотранспорта на 500 тыс. км. Снизили потребление электричества на 500 тыс. кВт в год.
Алексей Вершинин: Проект Henkel – это один из крупнейших проектов компании Jungheinrich в России. И этот проект действительно стал очень важным стартапом в секторе автоматизации.
После этого опыта мы можем однозначно сказать, что в этом сегменте мы ставим себе цель и имеем амбиции стать №1 в России. У нас имеются все предпосылки для этого.
Далее - ответы на вопросы участников пресс-конференции.
- Откуда и как поступали материалы для данного проекта?
Алексей Вершинин: Все материалы для данного проекта поступали только из Германии.
Транспортная логистика проекта была для нас большой задачей. Расстояния не маленькие. Напомню, что проект шел в Уральском регионе. Была непростая задача организовать поставки в Пермь, и одновременно заниматься вопросами монтажа. И команде пришлось работать слаженно, как часовой механизм для того, чтобы реализовать эту задачу.
Что касается транспортировки, в зависимости от того, где конкретно находился завод-производитель конкретных материалов, часть груза была поставлена фурами, а часть – судами до порта Санкт-Петербург, и затем отправлялась в Пермь.
Это действительно был большой объем груза – более сотни фур (контейнеров) были отправлены в Пермь. Все это надо было планировать очень четко, в жестких временных условиях. Поступало стеллажное оборудование, поступали транспортеры и погрузчики. Все это одновременно монтировалось. Сейчас мы приобрели весь необходимый опыт и можем однозначно сказать – да, это мы умеем делать, в том числе и в России.
- Кто выступил вашим конкурентом в Европе?
Алексей Вершинин: Компания SSI SCHAEFER. Всего в тендере участвовали 5 компаний (все из Европы). Российские компании пока не умеют реализовывать такие проекты и производить такие системы. И, конечно, это играет на руку европейским поставщикам.
Сергей Гордиенко: Да, в России нет местных компаний, которые могут предоставлять такого рода решения.
- Во сколько обошелся распределительный центр и сколько заработала компания Jungheinrich?
Сергей Гордиенко: Весь проект обошелся компании Henkel около 500 млн. рублей или 14 млн. евро.
Алексей Вершинин: Для нас особенно важно было реализовать этот проект. Самым важным для нас был имидж в рамках такого проекта.
- Каков срок окупаемости проекта?
Сергей Гордиенко: Расчетный срок окупаемости инвестиций в проект – около 3,5 лет. Для склада – это очень хороший срок.
- В каких продуктах все-таки больше компетенций у компании Jungheinrich?
Алексей Вершинин: Не важно, какое решение мы продаем клиенту. Важно, чтобы решение соответствовало потребностям клиента. В любом случае, один продукт только выигрывает от того, чтобы будет реализован другой продукт. Они все взаимосвязаны. Мы можем предложить клиентам весь спектр решений.
- Планируется ли запуск производства складской техники в России?
Член правления Jungheinrich AG Хельмут Лимберг: Таких планов у нас нет.
Читайте также по данной теме:
- Хельмут Лимберг о результатах 60-летней активной работы Jungheinrich в области внутренней логистики в мире и в России.
- Jungheinrich отметил 10-летний юбилей в России.
- Jungheinrich в России: 10-летняя история успеха.
- Немецкое качество услуг для клиентов по всей России.
Ырысбек Ташбаев, директор по развитию, Отраслевой портал «Логистика»
2 сентября 2013 года
Перепечатка статьи допускается с обязательной прямой гиперссылкой на главную страницу сайта www.logistics.ru или на страницу размещения статьи. При использовании в печатных изданиях – с указанием "Отраслевой портал "Логистика" и даты публикации.