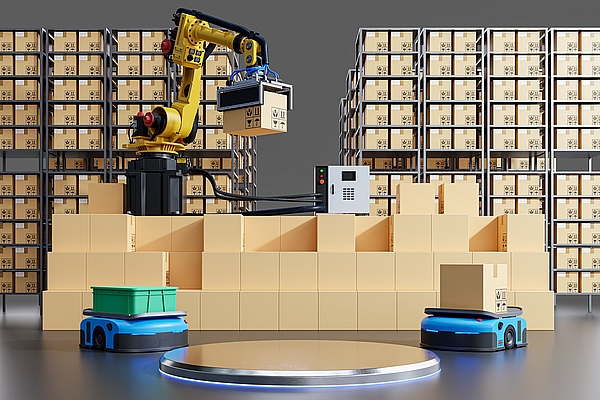
Руководитель направления систем бизнес-аналитики BIA Technologies Станислав Воронин рассказывает о цифровых двойниках, 3D-симуляциях и виртуальных экспериментах с логистикой. Это будущее уже наступило.
Последние два года российский рынок онлайн-торговли бьёт рекорды по темпам роста. Стремительное развитие сектора и возрастающие требования клиентов к доставке товаров привели к существенному увеличению спроса на складские и логистические услуги. Но открытие нового пространства — это долгий и затратный процесс, поэтому компаниям приходится заниматься оптимизацией текущих складов. Простым увеличением штата проблему тоже не решить — спрос повысился настолько, что склад просто не может переварить такой объём заказов. Другого выхода нет: нужно повышать эффективность, снижать издержки и оптимизировать операции.
К сожалению, это понимание пока пришло не ко всем игрокам индустрии. Некоторые компании вспоминают о желании повысить эффективность склада, когда метаться уже поздно: происходит всплеск продаж, существенно увеличивается товарооборот и отдельные элементы процесса дают сбой. В особо тяжёлых случаях это приводит к полной остановке деятельности склада и вытекающим из этого убыткам. Компании некогда искать оптимальное решение, и она идёт по экстенсивному пути — экстренно расширяет штат сотрудников и складские площади.
Дальновидные руководители задумываются о повышении эффективности склада заранее, не дожидаясь форс-мажора. Как правило, под эту задачу выделяется отдельный специалист — менеджер по развитию складских процессов. Традиционный подход к выработке мероприятий по оптимизации базируется на субъективной оценке и выборе конкретных инициатив. Ключевым фактором здесь служит накопленный опыт специалиста, который курирует изменения. На данный момент такой подход является базовым для большинства отечественных организаций, так как он практически не требует затрат на этапе планирования и может быть реализован внутренними ресурсами компании.
Но у традиционного подхода есть недостатки. В условиях динамично меняющейся внешней среды успешный опыт в прошлом ещё не гарантирует успеха в будущем. Кроме того, гипотезы приходится тестировать на реальных объектах. Ошибка в расчётах — и компания сталкивается с внеплановыми расходами. При внедрении дорогостоящих технических решений или конструктивных изменениях склада цена ошибки возрастает. Наконец, очевидно, что проверить сразу несколько конкурирующих идей одновременно в условиях реального склада практически невозможно. Обычно эксперименты проводятся в «низкий» сезон, чтобы минимизировать риски операционных сбоев на действующем объекте. Это может привести к неверной интерпретации результатов, поскольку низкий сезон на складе бывает только несколько месяцев в году.
Если вы читали предыдущие статьи в блоге, то наверняка догадываетесь, к чему я веду: супергерои-математики снова спасают Готэм-Сити, и на смену несовершенным расчётам в ручном режиме приходит точное компьютерное моделирование. В рамках складской логистики специалистов выручают цифровые имитационные модели.
Как это работает
1. As is: создаём цифровой двойник
Для начала аналитики тщательно исследуют оригинал — в данном случае, физический склад. Затем с помощью математических методов создаётся виртуальная копия, она же имитационная модель, существующих объектов и бизнес-процессов. Используя данные из WMS- или ERP-системы, модель детально описывает и отражает текущее состояние склада.
Перед началом использования виртуальной копии в практической деятельности проводится её валидация. На вход модели подаётся информация об объёме заданий, которые фактически имели место на складе в определённый момент времени, после чего реальные метрики производительности сравниваются с теми, что рассчитала модель. Если расхождения отсутствуют или минимальны, имитационная модель готова к использованию.
Для обозначения такой виртуальной копии принято использовать словосочетание «цифровой двойник» (digital twin). Это понятие относительно новое — впервые его практическое описание появилось в отчёте NASA о моделировании и симуляции 2010 года (там речь шла о виртуальной копии космического корабля). За какие-то десять лет цифровые двойники превратились из удивительной технологии будущего в первый шаг на пути к тотальной цифровизации и автоматизации всех процессов. В глобальных прогнозах на 2022 год эксперты американской исследовательской компании ABI Research называют массовое внедрение цифровых двойников трендом №1.
2. Bottlenecks: находим проблемы и точки роста
Модель склада As Is («как есть») позволяет объективно оценить текущее состояние логистических процессов и выявить узкие места (bottlenecks), ограничивающие работу склада. Так мы понимаем, какие участки нуждаются в совершенствовании и за что стоит взяться в первую очередь.
Приведу реальный пример: в рамках одного из проектов к нам обратился заказчик с проблемой регулярного превышения нормативного времени на складскую обработку грузов. Смоделировав текущее положение дел на складе, мы обнаружили расхождение более 10% во времени обработки машин на загрузку и выгрузку. Чтобы локализовать ошибку, мы более детально проанализировали данные за неделю работы. Оказалось, что проблема заключалась в ошибке алгоритма выбора ворот в рамках системы управления грузовым двором (YMS), предназначенной для автоматизации процессов управления транспортом на территории складского комплекса. Когда ошибку исправили, процессы удалось ускорить в среднем на 15%.
3. What if: тестируем гипотезы
Наиболее часто цифровая модель склада используется для проведения what-if-экспериментов. Они позволяют ответить на вопрос «Что будет, если...». Например, что если мы изменим расположение грузовых ворот, переориентируем маршруты передвижения по складу, увеличим грузопоток, скорректируем процесс обработки или наймём больше грузчиков. Цифровой двойник помогает протестировать все предлагаемые гипотезы с точной оцифровкой не только метрик локального сокращения потерь, но и общего изменения эффективности смежных процессов и бизнеса в целом. Верификация предлагаемых инициатив на основе цифровой модели позволяет находить оптимальное решение с целью максимального улучшения анализируемых параметров.
Приведу ещё один пример из личной практики. Склад заказчика не справлялся с объёмами грузов в пиковый сезон. При этом руководство склада довольно долго пыталось внедрить в работу терминал сбора данных, отвечающий за получение заданий (на перемещение, подбор и расстановку) и передачу актуальной информации в учётную систему по результатам выполнения. Наша модель выявила неоптимальный алгоритм назначения заданий — стартовая версия попросту не учитывала неравномерность нагрузок на ворота склада. Тогда мы протестировали три итерации алгоритма как в обычном, так и в пиковом режиме работы. По итогам экспериментов была выбрана наиболее перспективная версия алгоритма работы терминала и реализована его доработка.
4. What next: предсказываем будущее
На этом возможности цифровых двойников не заканчиваются. Если на вход имитационной модели подавать данные с WMS-системы в режиме реального времени, то можно не только оперативно отслеживать производительность, но и с высокой точностью прогнозировать возникновение узких мест или пиковых нагрузок на том или ином участке работы, а также формировать оповещения по изменению объёма и графика доступности ресурсов. Эта информация позволит руководителям заблаговременно запустить соответствующие упреждающие сценарии.
Данная технология может быть масштабирована вплоть до балансировки всей цепочки поставок, сквозным образом проходящей через ERP-, WMS-, YMS- и TMS-системы.
Один заказчик обратился к нам с проблемой низкой эффективности процессов отгрузки готовой продукции. Особенность компании — в значительной доле клиентов, которые осуществляют забор продукции самовывозом. Таким образом, невозможно предугадать, какие именно из средних и мелких заказов будут отгружаться в конкретный день, что приводит к очередям на территории складского комплекса и пиковым нагрузкам по сборке заказов. Для решения задачи первым делом были созданы цифровые модели склада и двора. На их основе была разработана интегрированная система оптимального управления отгрузками. Реализованная система позволяет на основании предварительно поданных заявок, либо по факту прибытия машины для получения товара, выстраивать очередь погрузки, определяя маршрут движения по территории, назначая ворота и формируя очередь на сборку заказов на склад. Дополнительно осуществляется мониторинг местоположений и статусов автомобилей на основании сканирования номеров на шлагбаумах, воротах и проходных.
Преимущества имитационных моделей
Плюсы применения цифровых двойников очевидны. Во-первых, виртуальные эксперименты с имитационными моделями обходятся гораздо дешевле и занимают меньше времени, чем эксперименты с реальными активами. Средний период внедрения модели — 1–3 месяца. Система поможет обнаружить проблему или уязвимость, определить последовательность внесения изменений и провести тестовый запуск процесса в кратчайшие сроки. Результаты анализа также можно учитывать при разработке дорожной карты развития логистики на длительный горизонт планирования.
Во-вторых, имитационная модель — это цифровой инструмент с понятным интерфейсом и панелью управления, которой может пользоваться человек без каких-либо глубоких познаний в математической оптимизации. Компьютерное моделирование даёт возможность визуализировать результат в любой удобной форме — от таблицы Excel до 2D- и 3D-симуляции, что делает любые идеи и концепции более наглядными.
Пример 3D-симуляции склада
Итак, в результате внедрения имитационного моделирования руководители и специалисты, занимающиеся вопросами повышения эффективности, получают инструмент, который позволяет проводить множество экспериментов, тестировать работу в условиях пиковых нагрузок, отрабатывать гипотезы по изменению структуры отгрузок и характера перевозимого груза, определять оптимальный объём требуемых ресурсов и многое другое. Причём все эти эксперименты и «краш-тесты» проводятся в безрисковой среде, не останавливая реальный бизнес-процесс. Меняя параметры цифровых двойников, логисты могут быть сродни генералам, которые передвигают фигурки воинов перед реальным сражением для того, чтобы выработать оптимальную тактику и стратегию.
Имитационная модель — действенный инструмент для решения задачи оптимизации логистики, пространственного планирования и повышения эффективности работы склада. Не зря этот подход применяют в рамках популярной сейчас концепции бережливого производства.
Впрочем, нужно понимать, что сама по себе имитационная модель не даёт указания по оптимизации и перестройке бизнес-процессов. Она не предлагает решения проблем, а лишь просчитывает эффект от внедрения того или иного решения, придуманного человеком. Чтобы цифровой двойник принёс желаемые результаты, его нужно встраивать в процессы изменения складской логистики, следить за получаемыми данными и правильно их интерпретировать. Для этого необходим бизнес-аналитик. Без должной компетенции имитационная модель останется красивой, но бесполезной 3D-картинкой.