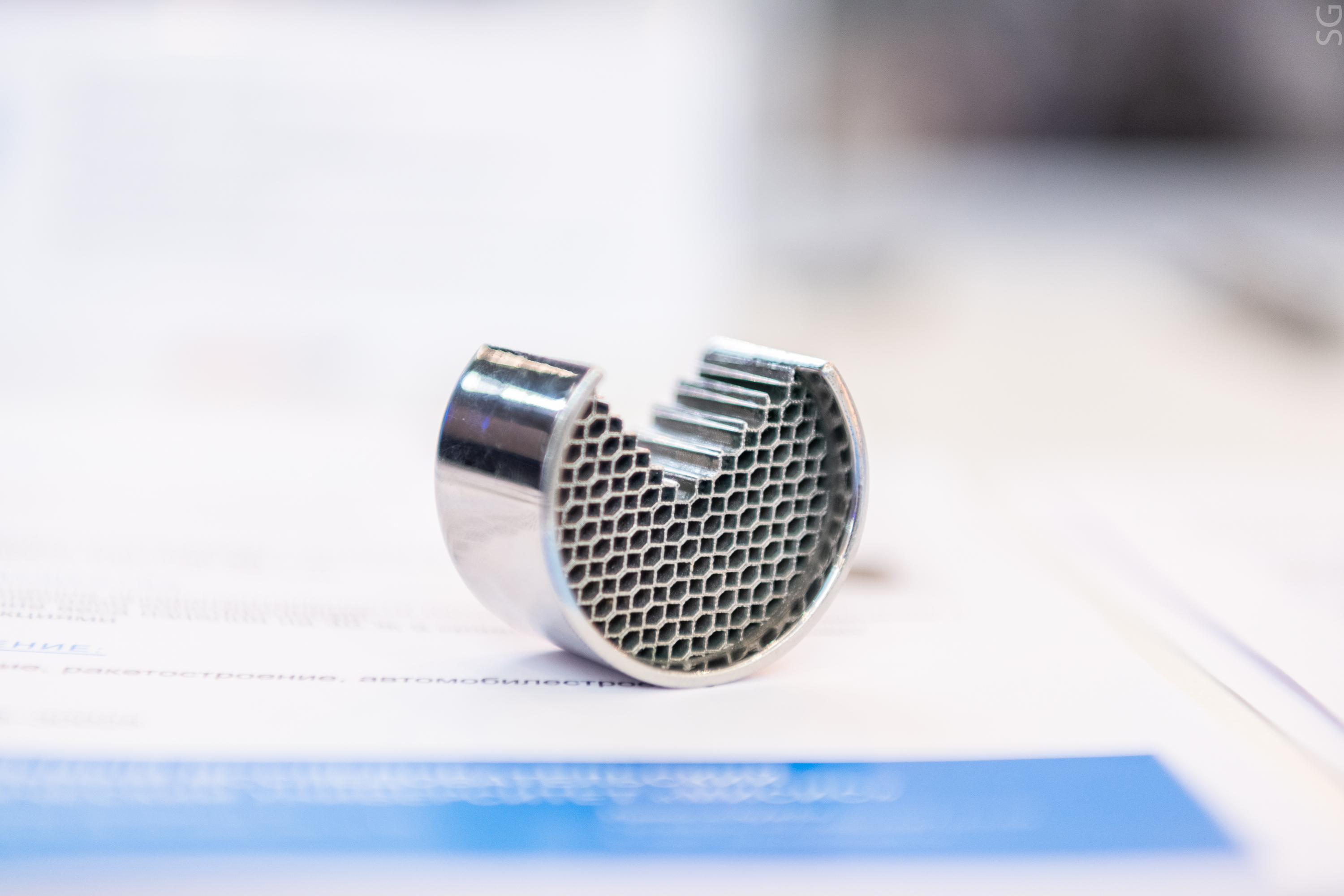
В рамках XVII всероссийского форума «ГОСЗАКАЗ» НИТУ «МИСиС» представил ряд готовых деталей для авиакосмоса и автомобилестроения из нержавеющих и цветных сплавов, полностью напечатанных на 3D-принтере. Некоторые из них невозможно изготовить традиционными методами. Разработанная учеными технология снижает себестоимость изделий и сокращает время производства в среднем на 30-50%.
Ученые НИТУ «МИСиС» вывели металлическую 3D-печать на новый уровень, представив универсальную технологию производства деталей, используемых в авиакосмической и авиационной промышленности, на одном 3D-принтере. В качестве основы был взят 3D-принтер российской компании Addsol, конструкция которого была оптимизирована и доработана инженерами лаборатории «Катализ и переработка углеводородов». Стоимость отечественного 3D-принтера в 2 раза меньше чем у иностранных аналогов.
Для печати одной группой металлов пришлось оптимизировать конструкцию принтера, для печати другими – модифицировать сами материалы при помощи полученных коллективом добавок и катализаторов. В итоге была получена уникальная система селективного лазерного плавления для получения 3D-образцов малых размеров из различных, зачастую весьма сложных в обработке, металлов и сплавов.
На форуме «ГОСЗАКАЗ» в Технопарке «Сколково» были представлены полученные с ее помощью реальные узлы для современного машиностроения с оптимизированными характеристиками.
Патрубок системы охлаждения, применяющийся в автомобилях, полностью полученный методом селективного лазерного плавления (SLM). Изготовить такую деталь возможно только аддитивным методом, так как толщина стенки изделия – 0,3 мм, у существующих аналогов – 2 мм.
3D-печать форсунки гидросбива окалины для металлургических производств позволила оптимизировать конструкцию изделия, сократив количество деталей с шести до одной монолитной.
«Пламегаситель, предназначенны
й для обработки, охлаждения и снижения скорости раскаленных выхлопных газов в авиа- и ракетостроении мы также синтезировали методом SLM, чем обеспечили уменьшение продолжительности изготовления на 50 % в и снижение веса изделия на 40% в сравнении с классическими конструкциями. Из титанового сплава был произведен востребованный в авиапромышленности теплообменник. Лазерное плавление позволило изготовить деталь за одну технологическую операцию вместо трёх», – рассказывает представитель группы разработчиков, младший научный сотрудник лаборатории «Катализ и переработка углеводородов» НИТУ «МИСиС» Станислав Чернышихин.
Еще одно из перспективных применений технологии, по мнению создателей, – печать постоянных магнитов из порошка ниодим-железо-бор. Они применяются для создания генераторов, электродвигателей в автомобильной и авиапромышленности. Производство таких магнитов традиционными технологиями – это многоступенчатый, дорогостоящий процесс. 3D-печать позволила сократить количество стадий синтеза и, в конечном итоге, уменьшить стоимость самой детали. Кроме того, аддитивное производство дает возможность синтезировать магниты не только в форме диска или параллелепипеда, а любой сложной формы.
В настоящее время коллектив тестирует режимы печати из бронзы и меди, которые могут использоваться, в частности, для ракетных двигателей, а также магниевых сплавов и чистого вольфрама.