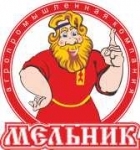
Логистический комплекс:
- 1500 тонн макаронных изделий
- 1056 м
- 200 наименований
- 1800 паллетомест
- 200 тонн поступление за 24 часа
- 200 тонн отгрузка за 12 часов
Валерий Кобылин, генеральный директор ОАО «ПКБ «Техноприбор»
Думаю, значение этого проекта существенно для всей российской интралогистики - в равной степени как для производителей оборудования, так и для потребителей. Проект, который мы реализовали для компании «Мельник», беспрецедентен для России. Впервые отечественной компанией запущен полностью автоматизированный склад, ни в чем, по большому счету, не уступающий лучшим зарубежным аналогам.
Безусловно, это не первый наш проект, мы профессионально работаем на рынке интралогистического оборудования с середины 50-х, но в то же время нам нечасто приходится иметь дело не с крупными государственными компаниями, а с частным капиталом, для которого приоритетное значение имеют высокие показатели эффективности.
Применение разнообразного автоматического оборудования получило широкое распространение в 80-е годы на большом количестве складских комплексов и крупных производственных предприятиях; проектные организации, в свою очередь, научились рационально использовать возможности техники. В то время мы создали множество систем, от применения которых отказалась стагнирующая промышленность после пересмотра государственного устройства. Сегодня мы можем сказать, что вновь вышли на тот уровень решаемых задач, который требует профессионального подхода, значительных интеллектуальных и производственных ресурсов.
Петр Яровой, директор по производству ОАО «Мельник»
Для нас принципиальное значение имеет рациональность и высокая эффективность при выборе технических решений, которые мы применяем на производстве. Поэтому мы еще в начальной стадии проекта по созданию новой макаронной фабрики предполагали использовать автоматическую технику на складе. Также мы испытывали определенные затруднения, связанные с возможными размерами пятна застройки. А именно, для сохранения удобного расположения относительно железнодорожных путей здание склада должно было быть вписано в существующие условия. Это накладывало ограничения на габаритные размеры склада. На тот момент мы еще не были уверены, что сможем найти производителя автоматической складской техники, который предоставит нам соответствующее нашему бюджету техническое решение. Поэтому мы решили строить здание, высота которого будет подходить для работы ричтраков, и одновременно вести поиск поставщика автоматизированного оборудования. На одной из промышленных выставок мы познакомились с компанией Техноприбор, как выяснилось позже - единственным в России производителем автоматических кранов-штабелеров и другого складского оборудования: конвейеров, грузоподъемных устройств и прочего. Техноприбор предложил нам создать проект комплексной автоматизации склада, включая разработку технологической части, проектирование и изготовление оборудования, программного обеспечения.
В результате было утверждено технологическое решение, которое удовлетворяло нас как с точки зрения объема хранимого товара, так и по параметрам грузооборота. Процессы приемки и отгрузки товара были автоматизированы. Существенно сократилась численность персонала, обслуживающего склад, например, ввод заявок теперь осуществляется всего одним оператором-кладовщиком. Все данные учитываются и хранятся в базе данных, тем самым гарантирована их сохранность и доступность в любое время.
Воплощение предложенной Техноприбором идеи оказалось даже несколько лучше, чем мы предполагали, так как установленная система управления автоматическим складом TechnoWMS дает возможность вводить дополнительные контрольно-учетные функции в действующую систему в зависимости от возникающих производственных задач.
Наша компетенция
- разработка технологии интралогистических объектов
- производство автоматического складского оборудования: кранов-штабелеров, монорельсовых транспортных систем, роликовых и цепных конвейеров
- организация управления складом
- модернизация устаревших автоматизированных складских систем
Описание
В основу проекта складского комплекса компании Мельник - производителя муки, зерна и комбикормов, легла задача создания высокоэффективного распределительного центра. Перед нашими специалистами были поставлены жесткие ограничения по площади и территориальному размещению склада. В относительно небольшом помещении - около 1200 м2 - нужно было организовать инженерный комплекс, способный обеспечивать существенный грузооборот, а именно - принимать 200 тонн готовой продукции в круглосуточном режиме и отгружать 200 тонн в течение 12 часов при объеме хранения около 1500 тонн. Таким образом, склад должен был иметь возможность полностью оборачиваться всего за 5-7 дней. Также существовали ограничения, заданные размерами помещения. К началу момента разработки технологической части проекта его уже начали строить, в связи с чем мы не могли влиять на первоначальные исходные данные.
В первую очередь нашими специалистами был проведен всесторонний анализ процессов с учетом особенностей, связанных с организацией физического перемещения грузов на планируемом складе и спецификой документооборота. Так же были проведены консультации с различными службами заказчика. Результатом стало техническое задание, которое давало представление о всех аспектах работы складского комплекса. Вместе со специалистами компании Мельник были расставлены приоритеты, и мы приступили к разработке технологического проекта.
Технология
Проанализировав параметры, в которых предстоит работать складу, наши специалисты пришли к выводу, что для обеспечения требуемой производительности необходимо автоматизировать не только зону хранения путем установки в ней автоматических кранов-штабелеров. Важным моментом является и автоматизация операций по приемке и отгрузке.
Учитывая необходимость размещения определенного объема груза, было принято решение разместить приемку и отгрузку на разных этажах мезонина, что позволило не только сэкономить место и разделить грузопотоки, но и оптимизировать алгоритм работы кранов-штабелеров, который практически полностью исключает холостые пробеги. Кран-штабелер, взяв груз согласно заявке, доставляет его к приемной секции конвейерной системы зоны отгрузки, после чего забирает вновь сформированную паллету во втором ярусе мезонина и размещает ее на стеллажах в зоне хранения. Следует также отметить, что автоматизированный склад одной стороной, на которой находится зона приемки, примыкает непосредственно к зданию фабрики. В настоящий момент фабрика оснащена тремя автоматизированными производственными линиями, конвейеры которых выдают уже упакованную продукцию на склад.
Единовременно на склад может поступать только 3 артикула. Далее следует единственная операция на всем складе, которая выполняется людьми, к тому же их участие сведено к минимуму. А именно - четверо грузчиков производят укладку упаковок с макаронами на паллеты, причем на одной паллете размещается только один артикул. После того, как грузчик собрал паллету, он дает команду о готовности нажатием всего одной кнопки на панели оператора. После этого подключается система контроля габаритов груза, и, если сформированный поддон соответствует заданным параметрам, система автоматически присваивает ему место размещения на складе согласно принципам, заданным системой управления складом (WMS); если нет - возвращает паллету грузчику для приведения ее в соответствие необходимым параметрам.
После сборки паллета с грузом отправляется по системе конвейеров в зону хранения, где работают краны-штабелеры, и размещается на стеллажах.
Отгрузка осуществляется также в автоматическом режиме. Для того чтобы начать отгрузку продукции, оператор вводит заявку, которая распределяется между всеми кранами-штабелерами, и они приступают к ее выполнению, доставляя паллеты с грузом на транспортную систему зоны отгрузки, по которой они могут быть поданы в разных направлениях - на отгрузку авто- и ж/д транспортом. Предусмотрена возможность одновременного выполнения заявок для авто- и ж/д транспорта: в данном случае система самостоятельно распределяет паллеты, подаваемые кранами.
Отгрузка в железнодорожные вагоны происходит при помощи специального конвейера. Упаковки с продукцией снимаются с поддона и отправляются по конвейеру в вагон, а освободившаяся паллета устанавливается на специальный подъемник для доставки пустых поддонов на второй этаж. Таким образом, паллеты не покидают склад, но возможность отгрузки вместе с паллетой предусмотрена.
Для погрузки автомобилей реализовано необычное решение: системой конвейеров, работающей на первом этаже в зоне отгрузки, паллеты доставляются в сторону автомобильных ворот и после этого поднимаются на лифте на второй этаж, где происходит их расформирование. Далее упаковки по склизу отправляются прямо в автомобиль.
Этот комплекс может отгружать до 5 автомобилей и 2 железнодорожных вагонов.
Таким образом было достигнуто выполнение условий по объемам принимаемой и отгружаемой продукции.
Оборудование
Все оборудование для реализации этого проекта было разработано специалистами в нашем собственном инженерном центре и изготовлено на заводе нашей компании. Для нас важно полностью контролировать процесс создания оборудования, так мы можем довести до совершенства все этапы и быть уверенными в результате.
Все оборудование, использованное в проекте, было специально предназначено для работы с палетой, с учетом того, что на палетах располагаются мешки с макаронами, которые не всегда имеют одинаковую укладку. Комплекс примененных мер гарантирует сохранение целостности даже столь неустойчивому грузу. Более того, предусмотрена возможность отгружать продукцию вместе с палетой и без.
Штабелер-автомат, предназначенный для размещения груза в зоне хранения и его подачи на отгрузку, работает в полностью автоматическом режиме. Оснащается системами автоматического управления, информационного обеспечения и безопасности и поставляется в комплекте с подкрановыми путями, системой кабельного питания и электроустановочной аппаратурой.
Стеллажный блок представляет собой фронтальные полочные стеллажи, оснащенные дополнительными связями и усилениями, дающими возможность работы в условиях дополнительных динамических нагрузок, создаваемых автоматическим краном-штабелером. Все стеллажное оборудование предоставлено российским производителем, изготовлено с использованием современных технологий, позволяющих обеспечить точностные параметры, необходимые для работы автоматических кранов-штабелеров.
Транспортер цепной приемно-подающий - транспортный элемент, предназначенный для подачи грузовых единиц в зону работы крана-штабелера с роликового конвейера.
Конвейер роликовый реверсивный - с его помощью грузовые единицы перемещаются между армами, на которых происходит укладка, и цепными передающими устройствами, с которыми взаимодействуют краны-штабелеры в зоне приемки. Также с помощью конвейеров паллеты направляются на отгрузку.
Подъемник с роликовой секцией поднимает и передает палеты для последующей отгрузки на автотранспорт, оснащен роликовой приводной секцией.
Подъемник для палет представляет собой грузовой лифт, предназначенный для возврата пустых поддонов в зону приемки для их последующего использования.
Устройство динамического контроля габаритов - устанавливается на местах сборки палет и проверяет габаритные характеристики поддонов перед отправкой в зону хранения, таким образом предохраняет систему от возможных сбоев, вызванных отклонениями от допустимых размеров.
Система управления
Система управления складским комплексом включает в себя два уровня. Первый уровень управляет аппаратной частью системы, посредством программируемых логических контроллеров отвечает за работу приводов, датчиков, блокировок, системы позиционирования.
Все основные функции управления складом осуществляются при помощи программы верхнего уровня TechnoWMS, являющейся нашей собственной разработкой, которая создавалась с учетом особенностей работы в автоматизированном складе.
Основные функции:
- документооборот
- интеграция с системой бухгалтерского учета
- учетная функция
- управление приемкой и отгрузкой
- различные формы статистической отчетности
- принципы размещения груза в зоне хранения
- принципы выполнения заявок на отгрузку
- возможность работы в автоматическом и полуавтоматическом режиме
- самодиагностика
Применение TechnoWMS позволяет наиболее полно использовать функциональные возможности автоматизированного склада в части управления грузооборотом за счет определения принципов, согласно которым будет производиться размещение груза в зоне хранения и отгрузка. В основе таких принципов могут лежать результаты ABC анализа, например, в зависимости от сезона или сроков производства продукции. Система позволяет оптимизировать документооборот, использовать такие возможности, как создание учетных записей и авторизация пользователей с различными статусами и уровнем полномочий, логировать все события, в том числе ошибки и сбои. Предусмотрена интеграция с бухгалтерским программным обеспечением и возможность создания отчетов в режиме реального времени.
Экономика
Существует суждение, что автоматизация на складе предполагает всегда значительно более существенные вложения, чем в случае использования напольного транспорта. Но, к сожалению, не все проводят расчет не только первоначальных капитальных вложений, но и эксплуатационных затрат, которые они понесут в ходе работы склада. В структуру эксплуатационных расходов войдут следующие статьи:
- заработная плата операторов работающих в зоне хранения
- техническое обслуживание ричтраков
- освещение
Примерный расчет заработной платы операторов ричтраков в проекте склада компании «Мельник» в случае использования напольного транспорта приведен ниже в таблице. С учетом особенностей работы склада влияющих на численность персонала. Такими параметрами будут являться:
- режим работы, в данном случае приемка ведется круглосуточно в 3 смены, отгрузка в 2 смены, 26 дней в месяц
- грузооборот определяет количество штабелеров или ричтраков, в данном случае 5 штук
Таким образом, для выполнения этих условий общий фонд рабочего времени составит 120 часов в день или 3180 в месяц. Если для расчета взять продолжительность смены 8 часов, то для того чтобы выполнить работу, потребуется около 18 человек. Предположим, что заработная плата одного оператора составит 20 000 р, а с учетом налоговых отчислений около 25 000 р. Причем мы не учитываем кладовщиков, которые потребуются вне зависимости от выбранной технологии.
Получается, что только в отношении персонала эксплуатационные затраты выше на 5 400 тыс. руб. в год. Это значит, что эффективность автоматической технологии выше, а риски, связанные персоналом и возможными изменениями экономических условий, ниже, так как для осуществления деятельности требуется меньший трудовой ресурс, и, соответственно, такой показатель, как точка безубыточности, имеет меньшее значение.
Дмитрий Вергунов, инженер отдела маркетинга
Техноприбор ОАО
info@technopribor.com
www.technopribor.com