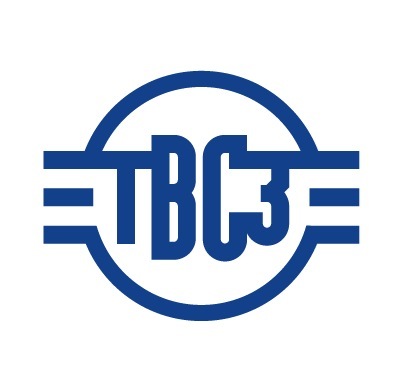
Накануне своего 10-летия в России Jungheinrich рассказывает об одном из своих крупнейших проектов на отечественном рынке.
В 2013 году немецкий производитель складского оборудования Jungheinrich отмечает десятилетний юбилей в России. Сегодня компания располагает офисами в Москве, Екатеринбурге, Санкт-Петербурге и Новосибирске, а также имеет сервисные отделения в 65 городах страны. За годы работы в России Jungheinrich воплотил десятки успешных проектов разного масштаба и уровня сложности. Об одном из них – уникальном как для России, так и для Европы, - рассказывают специалисты Jungheinrich в Санкт-Петербурге.
30 января 2012 года при участии Владимира Путина состоялся запуск вагоносборочного производства Тихвинского вагоностроительного завода – одного из самых современных в Европе промышленных объектов в сфере машиностроения. Производство Тихвинского ВСЗ обеспечивают 200 единиц складской техники от компании Jungheinrich. Этот проект стал одним из самых масштабных за всю историю работы немецкого концерна в России, и аналогов ему на отечественном рынке интралогистики сегодня не существует.
О значимости завода для российской промышленности лучше всего говорят цифры: общая территория составляет 50 га, из них производственным помещениям отводится 233 тыс. м2 при этом завод обладает мощностью для изготовления 13 тыс. вагонов, 65 тыс. колесных пар и 90 тыс. т стального литья в год. По официальной информации, общий объем инвестиций в создание завода составил более 30 млрд. руб. Продуктовая линейка завода насчитывает 11 типов вагонов, которые можно объединить в четыре основные категории: полувагон с глухим кузовом и универсальный полувагон с разгрузочными люками, использующиеся преимущественно для перевозки руды, угля и металла, вагон-хоппер – для транспортировки минеральных удобрений – и вагон-платформа для крупнотоннажных грузовых контейнеров длиной 80 футов.
История завода началась в 2004 г., когда инвестиционной группой ИСТ был представлен проект по созданию нового высокотехнологичного предприятия на территории Тихвинского производственного объединения «Кировский завод», который во времена СССР считался промышленным центром Северо-Западного региона. В январе 2008 г. началось строительство завода, и уже в июле было введено в эксплуатацию экспериментальное производство мощностью 100 вагонов в год, а в августе выпущены образцы полувагонов с разгрузочными люками.
Стремительный рост предприятия диктовал необходимость мощной логистической поддержки, и генеральный подрядчик приступил к поиску надежного поставщика складского оборудования.
«Проект потребовал поставки всех видов техники, которую мы производим»
Перед поставщиком техники стояли три основные задачи. Во-первых, у него должен быть в наличии широкий модельный ряд техники – от стандартных противовесных вилочных погрузчиков до высокопроизводительных узкопроходных штабелеров. Многоэтапный процесс производства нуждался в привлечении вспомогательной техники разных типов – для работы с паллетами, длинномерными и крупногабаритными грузами. Кроме того, высокие темпы строительства и запуск новых производственных цехов требовали оперативной поставки нескольких десятков единиц техники одновременно. И, наконец, поставляемые машины должны были пройти серьезную техническую адаптацию под нужды производства ТВСЗ.
Фактически поставщик должен был быть способным создать уникальные модели погрузочных устройств на основе своей продуктовой линейки специально для завода. Число поставщиков, которые могли бы удовлетворить всем требованиям проектировщиков, оказалось ограниченным, и в конечном итоге выбор генерального подрядчика пал на продукцию немецкого концерна Jungheinrich.
Менеджер Jungheinrich по работе с ключевыми клиентами в Северо-Западном регионе Илья Деркач вспоминает: «Проект потребовал не только предоставления практически всех видов техники, которую мы производим, но и привлечения самых сильных специалистов Jungheinrich в России. Также в сферу нашей компетенции входил поиск субподрядчиков - прицепы, которые отвечали бы техническим параметрам, в России найти не удалось, и мы закупали их напрямую из Германии». По словам его коллеги Юрия Легочкина, менеджера Jungheinrich по продажам системной техники, помимо предоставления заводу складской техники, немецкий производитель обеспечил комплексную поставку различных типов стеллажного оборудования.
Первая партия техники в количестве 78 ед. в основном состояла из тягачей и погрузчиков. Сегодня на Тихвинском вагоностроительном заводе работает более 200 ед. техники Jungheinrich.
Номерной знак – на каждом погрузчике
Территория вагоносборочного производства располагает двумя главными логистическими входами, через которые происходит отгрузка материалов для производства – их обслуживает 6 погрузчиков Jungheinrich, а само производственное помещение разделено на несколько цехов. В цехе сборки тележек и колесных пар изготавливается несущая часть вагона, здесь работают три узкопроходных штабелера ЕКХ 513 с поднимающейся кабиной, два тягача EZS 6250 и пять погрузчиков DFG 435 и EFG 316.
Отличительной особенностью погрузочной техники на ТВСЗ является наличие государственного регистрационного знака на корпусе каждого погрузчика. «Вся техника поставлена на учет в ГИБДД в соответствии с российскими нормами, при этом операторы проходят ежегодное освидетельствование. Перед выходом на смену операторы проходят предрейсовый медосмотр и получают допуск к управлению транспортным средством от медработника и главного механика», – говорит Сергей Загорский, начальник цеха логистики сборки тележек и колесных пар.
Между промежуточными складами курсирует погрузочная техника разных типов – для работы с различными номенклатурными группами товара. Цех сборки и сварки кузовов вагонов оснащен роботизированными линиями сборки люкового полувагона, вагона-платформы, полувагона с глухим кузовом и вагона-хоппера. Это самый насыщенный производственный передел. С июля 2012 г. предприятие начало отгрузку готовых вагонов потребителям.
На предприятии используется стеллажная система хранения, разработанная Jungheinrich. «Емкость стеллажей составляет более 5,4 тыс. паллетомест, а максимальная высота – 5,4 м, что соответствует российским стандартам пожарной безопасности. При этом стеллажная система статически рассчитана на возможность увеличения высоты в случае необходимости», – подчеркивает Юрий Легочкин. Обслуживают стеллажный комплекс 5 узкопроходных штабелеров ЕКХ 513 на рельсовой направляющей с использованием RFID-меток.
«Мы видим, насколько серьезен подход Jungheinrich к работе. Уверен в перспективе нашего взаимовыгодного сотрудничества», – заявляет Сергей Загорский.
В сентябре Jungheinrich планирует проведение пресс-конференции, приуроченной к юбилею, в рамках которой специалисты более подробно расскажут о сотрудничестве с ТВСЗ и о других значимых проектах концерна в России.
Статья предоставлена компанией Jungheinrich